The Healthcare Industry is Constantly Evolving
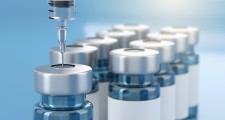
HARTFORD, Wis., September 4, 2020 (Newswire.com) - The healthcare industry is ever-changing and has, in the recent past, witnessed an increasing need for enhanced medical technology and portable devices which are durable. Similarly, the market for high performing medical components that are sustainable and compatible with the human body has also been on the rise. With CIREX investment castings, businesses can take advantage of each of these alloys.
Over the years, most medical equipment manufacturers have relied on stainless steel for production. Aluminum and cobalt are the latest entrants in the medical equipment market. CIREX investment castings are designed with precision cutting to help their customers get the best from these two alloys. CIREX products are made to be highly tolerant to give customers the performance that is second to none in the industry.
Stainless steel alloys for medical-grade equipment
The medical industry is ever-evolving thanks to innovations in material use. However, stainless steel remains the material of choice among most equipment manufacturers owing to its properties in biocompatibility, strength and high resistance to low and high temperatures. Players in the medical equipment manufacturing field can integrate all these dynamics to produce reliable and high-performance equipment. At CIREX, they have various alloys of stainless steel including chromium, nickel and carbon. CIREX has the 300 and 400 stainless steel series to help in every application.
The 400-series features 25% nickel, 11-27% chromium and 1% carbon while the 300-series stainless steel contains 16-30% chromium and 6-25% nickel. The 400-series is the best option for a high-strength material that is more affordable. The 300-series is the best for applications that require high corrosion resistance, high strength and temperature resistance.
Aluminum alloys for Class 1 & 2 devices and housings
Even though stainless steel has the right biocompatibility and strength credentials for Class 1 and 2 medical devices, it has low usability scores due to weight. It costs much less to manufacture aluminum alloys, plus they score highly on strength to weight ratio relative to stainless steel. Aluminum is also superior in preventing oxidation since aluminum oxide will eventually be formed, which creates a protective layer, which helps make the component firm. Lightweight aluminum continues to be used in making durable medical equipment, which is lightweight, easy to use and has been approved by the FDA.
Cobalt alloys (ASTM-75) for implantable devices
CIREX substitutes stainless steel with cobalt alloys, more so in the manufacture of implantable devices. Compared to other metals, cobalt-chromium can withstand high temperatures, corrosion, has a high resistance to wear and tear and is ferromagnetic. Cobalt-chromium is also ideal for implantable devices since it is 100% biocompatible.
Medical component manufacturer
Components of medical devices, be it Class 1 or 2, are required to comply with the standards set internally or by the regulatory authorities to ensure product safety and efficiency. Reach out to one of the metallurgists at CIREX to help establish the material that best suits specific medical requirements.
Source: CIREX