Refurbishment Extends Cooling Tower Life by 20 Years
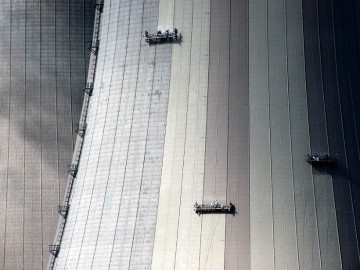
Isando, Johannesburg, South Africa, December 5, 2014 (Newswire.com) - An industrial cooling tower’s life expectancy is between 15 and 25 years, yet it is not always necessary to install a completely new system; old cooling towers can be refurbished or upgraded at a fraction of the cost. Refurbishment or upgrades can bring a cooling tower’s components up to original factory specifications, extending the system’s lifespan for another 15 to 20 years.
Over time, the humid environment of a cooling tower naturally leads to the build-up of contaminants resulting in clogging of the heat transfer medium and corrosion of metallic components. This build-up diminishes the efficiency of the cooling system and in severe cases can result in the collapse of the cooling tower structure. Plastic components gradually deteriorate over the operating life of the cooling tower becoming brittle and are therefore easily damaged due to maintenance activities or exposure to high winds and icing during winter.
Metal or wood cooling tower components can be cost-effectively replaced with parts made out of GRP. GRP components have a longer life expectancy when compared to a variety of construction materials, making them exceptionally economical over the long run.
Roger Rusch, CEO of Industrial Water Cooling (IWC)
Cooling tower refurbishment is achieved by cleaning the inside of the cooling tower and all metal parts, using sandblasting to remove corrosion. Once sandblasting is completed, an epoxy coating is applied to the metal, with a flexible epoxy stripping applied to the joints to allow flexibility and prevent leaking. Once the process is completed, the cooling tower will look and operate like new.
During the refurbishment, it is often necessary to replace fill media. Inside a cooling tower, the fill is the medium used to put as much water surface area in contact with as much air as possible for the longest amount of time possible. Water is cooled as it trickles down the fill medium, thus aiding the heat transfer process.
The almost constant exposure to water with high temperatures leads to wear and tear, particularly in older cooling towers that use wood as fill media. Wood fill media can be replaced with more suitable non-clogging fill materials such as splash or trickle packs.
Says Roger Rusch, CEO of Industrial Water Cooling (IWC), “PVC film-packs are the most commonly used type of packing in smaller industrial cooling towers. These are strong, resistant to chemicals and efficient. The softening temperature of PVC-fill material is 60°C, and we therefore advise that the maximum temperature of water entering the tower should not exceed 60°C and the continuous operating temperature should be less than 55°C."
“Where temperatures consistently exceed 60°C, operators should consider replacing fill media with a stainless-steel, non-clogging X-Grid splash pack. The X-Grid is also resistant to erosion, and there is no aging effect as found on plastic fill types. This pack can be steam cleaned, making it easy to maintain. The HDPE (High Density Polyethylene) Tubular Trickle pack is recommended for use in cooling water with a high solid content where film packs would be easily clogged. The individual tubes can be removed for cleaning and re-installed with ease.”
Refurbishment of cooling tower components with GRP elements is a cost-effective method to achieve maximum efficiency. Glass-reinforced plastic (GRP) is a modern composite material that is exceptionally strong, durable, and corrosive resistant. Due to its unique physical properties, GRP can be easily moulded and manufactured to meet almost any cooling tower specifications. For these reasons, it is the ideal material to consider when refurbishing a cooling tower.
Says Roger Rusch, “Metal or wood cooling tower components, including fan rings, distribution launders and troughs, inlet louvers, pipes, fan impellers and fan stacks, can be cost-effectively replaced with parts made out of GRP. GRP components have a longer life expectancy when compared to a variety of construction materials, making them exceptionally economical over the long run.
“IWC has extensive experience in maintenance and refurbishment of cooling towers and specialises in cooling tower thermal upgrades. Our patented online refurbishment technology ensures that operational natural draught cooling towers do not have to be taken out of service during the maintenance process. We have successfully employed this technology in a number of natural draught cooling tower refurbishment projects – including projects for SASOL (Secunda) and EnergyAustralia.”