Clarke Valve Optimizing Bolting Configurations in Pressure Vessels in an Effort to Reduce Size and Weight
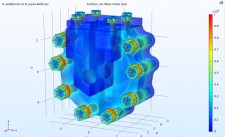
NORTH KINGSTOWN, R.I., February 12, 2020 (Newswire.com) - Control valve standards and guidelines (specifically ASME B16.34), which have been in place for over 50 years, have undergone incremental changes. These standards are important as they prevent field failure by maintaining system performance and ensuring the safety of workers and other components in proximity to valves.
New control valve technologies represent a significant alteration in valve geometry and operating characteristics. During the development, the valve body geometry and design requirements were closely examined. The authors have identified opportunities for adjustments to ASME B16.34 design requirements through the review of related standards and the process of design optimization.
Specifically, this paper reviews the design requirements for valve body joints and their bolting configurations. It examines bolt properties, including yield stress, proof strength, and allowable stress, through the ASME Boiler and Pressure Vessel Code [1], ASME B16.34 [2], ASME B16.5 [3], and ASME B31.3 [4].
It is proposed that the design requirements found in ASME B16.34 Section 6.4, Valve Joints, be adjusted such that the allowable stress limit for high strength bolts can be fully utilized.
Finite Element Analysis is performed to examine those dynamic loading scenarios that are accounted for in the determination of allowable stress - temperature gradients (which cause pipe expansion and contraction), cyclic fatigue, vibration, impact (flashing or hydraulic shock), seismic events, and live loads (ice/snow).
Data from the analysis is presented to show that the modified bolting configuration can withstand the maximum pressure and temperature requirements. Alternative bolting configurations can be shown to conform to the allowable stress requirements, allowing for design optimizations that reduce the overall size and weight of a valve.
Modifications to ASME B16.34 and ASME B16.5 are therefore recommended. When the proposed bolting configuration was applied to a DN25 valve, we were able to achieve weight savings of 4 lb, along with a 0.6” reduction in outer diameter. These optimizations allow for manufacturing cost savings, including cost of hardware, raw materials, and machining. This optimization can be extrapolated for greater savings with larger valve designs.
Mancovsky, Justin, and Ferriera, Jarod. "Optimizing Bolting Configurations in a Pressure Vessel." Proceedings of the ASME 2019 International Mechanical Engineering Congress and Exposition. Volume 14: Design, Systems, and Complexity. Salt Lake City, Utah, USA. Nov. 11-14, 2019. V014T14A022. ASME. https://doi.org/10.1115/IMECE2019-11561
About Clarke Valve
Founded in 2011, Clarke Valve™ provides high-quality industrial control valves to organizations worldwide and is a portfolio company of Saudi Aramco Energy Ventures, Chevron Technology Ventures, and OGCI Climate Investments. Using aerospace design principles, Clarke has developed the Shutter Valve™, validated by the Oil & Gas industry as a highly reliable and important innovation in control valve technology. The Shutter Valve is one of the few control valves that achieves both API 641 and ISO 15848-1 low fugitive emissions certifications. The Shutter Valve by Clarke Valve is the world’s most compact, efficient, and environmentally responsible control valve. Clarke Valve technology is currently deployed in a diverse spectrum of markets, including oil and gas, aerospace, chemical, power plants, and water management.
For media inquiries, please contact Emma Peterson, Sales Coordinator, at emma.peterson@clarkevalve.com
Source: Clarke Valve